AN ENDLESS ARRAY OF OPTIONS
WE ENSURE
ŠIROKA PALETA BOJA OTPORNIH NA UV ZRAČENJE
Thrill.
Get attention. Stand out.
We adapt to each customer through the production process. We develop the colour of the RAL scale in a very short time. The extensive colour palette, from classic to non-traditional colours, inspires and attracts attention, and helps designers and architects in creating modern projects for hospitals, operating rooms and laboratories.
SEE ALL COLOURS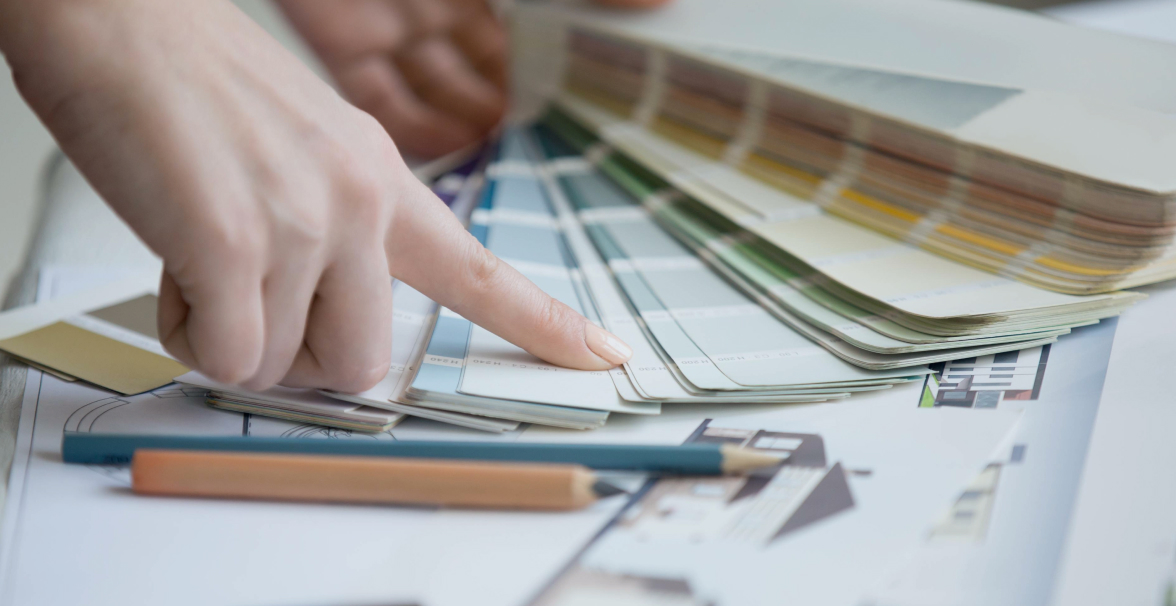
PLANNING AND EXECUTION
Physical properties
Property | Value | Method |
Density | 1,68 – 1,75 g/cm³ | SIST EN ISO 1183 – 1/A |
Approximate weight per m² for d = 6mm | 10,2 kg | |
Approximate weight per m² for d = 12mm | 20,4 kg | |
Coefficient of linear thermal expansion | 3,7 x 10⁻⁵ K⁻¹ | Α (-20 °C do +50 °C) |
Barcol Hardness | 58 – 64 | SIST EN 59 |
Mechanical properties
Property | Value | Method |
Flexural modulus | 8800 – 9800 Mpa | SIST EN ISO 178 |
Flexural strength | 50 -71 Mpa | SIST EN ISO 178 |
Tensile strength | 29 – 53 Mpa | SIST EN ISO R 527-1 |
Elongation at break | 0,5 – 0,9 % | SIST EN ISO R 527-1 |
Toughness | 3,0 – 5,5 Kj/m² | SIST EN ISO 179-1 |
Električne lastnosti
Property | Value | Method |
Surface resistivity | 2,0 x 10¹¹ – 2,0 x 10¹² | DIN VDE 0303-3 IEC 93 |
Specific volume resistivity | 7,9 x 10¹³ – 1,2 x 10¹⁴ Ωcm | DIN VDE 0303-3 IEC 93 |
Resistance to tracking currents | CTI 600 M | DIN VDE 0303-1 IEC 112 |
Relative dielectric constant (εᵣ) | 4,5 | DIN VDE 0303-4 IEC 250 |
Dielectric loss factor (tan δ at MHz) | 2,8 x 10⁻³ | DIN VDE 0303-4 IEC 250 |
Other properties important for use
Property | Value | Method |
Water absorption (after 24 hours) | 0,03 % | SIST EN ISO 62 metoda 1 |
Resistance to water vapour effects (1 hour) | Level 4 – small change in shine, only visible under certain angles | SIST EN 438-2 |
Resistance to hot container effects | Level 4 – small change in shine, only visible under certain angles | SIST EN 438-2 |
Resistance to burning cigarette effects | Level 4 – small change in shine, only visible under certain angles | SIST EN 438-2 |
Resistance to atmospheric agents | No change | 2-year outdoor exposure |
Classification of material response to fire | B-s1, d0 | SIST EN 13501-1 |
Harmlessness to health | Corresponds to | Article 3 of the Regulation of the European Parliament and Council (EC) No. 1935/2004 on the materials and articles intended to come into contact with foodstuffs |
*The data do not apply to EC and MF plates.
The load-bearing substructure represents the bond between the concrete base or load-bearing wall and the exterior wall cladding, and allows load transfer between the two. The exterior cladding is constantly exposed to weather conditions (fluctuation of temperature, humidity, wind, etc.) and may deform slightly (linear elongation) under such conditions due to its composition and technical properties. An adequately designed installation of substructure enables all such deformations to occur without causing additional tensions, noise and damage to the joints and cladding. The substructure elements also allow three-dimensional adjustment, which enables the exterior cladding to be installed completely flat.
BASIC COMPOSITION OF THE VENTILATED FAÇADE
A ventilated façade is essentially a multilayered and multi-function system. The outer layer or Kerrock cladding protects against external influences and lends the building an aesthetic look, while the inner layers and substructure provide firmness, ventilation, and both thermal and sound insulation.
An outline of the basic composition of the ventilation façade.
SUBSTRUCTURE
The load-bearing substructure represents the bond between the concrete base or load-bearing wall and the exterior wall cladding, and allows load transfer between the two. The exterior cladding is constantly exposed to weather conditions (fluctuation of temperature, humidity, wind, etc.) and may deform slightly (linear elongation) under such conditions due to its composition and technical properties. An adequately designed installation of substructure enables all such deformations to occur without causing additional tensions, noise and damage to the joints and cladding. The substructure elements also allow three-dimensional adjustment, which enables the exterior cladding to be installed completely flat.
For the installation of Kerrock cladding, standard façade substructure systems made of aluminum are used. These meet all structural, construction, and statics requirements.
The widest spacing between vertical studs in a grid is max. 74cm. The maximum permissible wind load for a 74 × 74cm grid is 3.50 kN/m2. In case of heavier loads, the spacing of the grid must be reduced.
HEAT INSULATION AND VAPOUR PERMEABLE WALL WRAP
Thermal insulation, produced in accordance with SIST EN 13162, must be made of non-combustible mineral fibres. Mineral or stone wool is recommended because it is solid and formed in panels and slabs. In addition, it enables simple remodeling to desired dimensions. The thermal insulation is anchored onto the concrete base or load-bearing wall and the insulation thickness can be between 5 and 30cm.
A vapour permeable wrap is laid on top of the thermal insulation to prevent water from entering the thermal insulation and to control the moisture and heat transfer. This prevents damage to the thermal insulation, as the excess water then evaporates in the ventilation layer. The integrated vapour permeable wrap offers good thermal protection as well and has the ability to diffuse water vapour.
FIXING THE OUTER LAYER OR CLADDING
The outer layer in the ventilated façade is made of Kerrock material, where Kerrock panels of different dimensions are used as external façade elements.
The finishing layer or Kerrock cladding is fixed onto the substructure using the SikaTack®–Panel adhesion system. This system is tested and certified, and its elasticity allows for a slight deformation of the cladding resulting from external influences (temperature, humidity, wind …).
Fixing the panels using an elastic system instead of bolts prevents high voltage in the panels as well as galvanic corrosion, and allows the bonding of materials with different linear elongations.
In addition to elasticity, a great advantage of glued façades is the aesthetic element, as there are no visible clamps typical of hung façades or rivets typical of riveted façades.
VENTILATED FAÇADE SYSTEM WITH GLUED CLADDING
The Kerrock ventilated façade system is shown on the horizontal cross-section in Figure 1. The base aluminum substructure is mounted onto the concrete base using a fastening screw. A layer of heat insulation made of non-combustible materials is then inserted, whereby an air layer is created between the cladding and the thermal insulation, in order to ventilate and remove moisture.
However, Kerrock sheets or panels are used for the outer layer or cladding; these are attached to the substructure by means of an adhesion system.
Horizontal section of a typical ventilated façade system with glued cladding.
The presence of a ventilated air layer distinguishes ventilated façades from regular façades. Their advantages are better moisture removal in winter and less overheating of the building in summer. At that time, the cladding heats up and the air layer prevents heat transfer to the thermal insulation.
Kerrock cladding can also be installed on top of uneven surfaces, since the properties of the Kerrock material permit thermal deformation and bending.
Due to the relatively high potential bending and dimensional instability, the installed Kerrock panels must be subject to periodical inspections performed by qualified persons. The maximum inspection interval of the condition and functionality of the façade assembly containing the Kerrock panels is 5 years. At the inspection, it is necessary to check the permanent deformations, any potential damage to the panels, and the condition of the glued joint (visual inspection).
Damaged parts which are essential for the stability and functionality of the façade assembly, should be replaced immediately after the potential damage. Only spare parts complying with the technical approval provisions (STS 11/0024) can be used for replacement. During use, maintenance and cleaning of the façade assembly, it is necessary to follow all the additional instructions of the manufacturer.
SPECIFIC BUILDING-CONNECTED ORDERS
The production of Kerrock cladding elements is carried out using natural raw materials, which can affect the colour tone in each individual batch.
It is important that the façade cladding elements for a particular building are ordered together, as this is the only way to ensure no differences in colour shades between individual panels arise, since all the supplied panels will come from the same batch.
The supplier shall provide a 10-year warranty for the Kerrock façade panels, which shall start on the day of delivery, subject to the following conditions:
- if the façade panels were cut and drilled at the factory (transport and storage) in accordance with the recommendations in the technical documentation and instructions in force at the date of delivery of the KERROCK façade panels and
- if the façade panels were installed in accordance with the instructions for fixing the KERROCK façade panels, using the supplied original fixing materials (clamps, adhesives, adhesive tape, etc.).
The warranty does not cover errors that occur or are caused by:
- inadequate treatment and storage at the construction site, reshaping and installing the panels, unauthorised contractors, or
- inadequate use of façade panels with regard to local conditions and requirements
no. | TESTED BY/ISSUED BY | SHORT SUMMARY |
1. |
Slovenian Technical Approval STS-11/0024 for Kerrock panels for glued façade and wall cladding, awarded on the basis of the provisions of the Act on Construction Products – ZGPro. ZAG – Zavod za gradbeništvo (“Slovenian National Building and Civil Engineering Institute”). Ljubljana, 2017. | The product complies with the Law 1 and Rules 3, from this STS. |
2. |
EXOVA Warringtonfire, Testing of smoke development and toxicity to certificate the flammability characteristic according to Resolution 61. (67), FPT Code, Annex 1, Part 2, Frankfurt am Main 2011
|
Kerrock, as a waste product after incineration, can be disposed of at an orderly landfill without any preceding treatment. There are no toxic elements in the eluates. |
Advantages of a ventilated façade
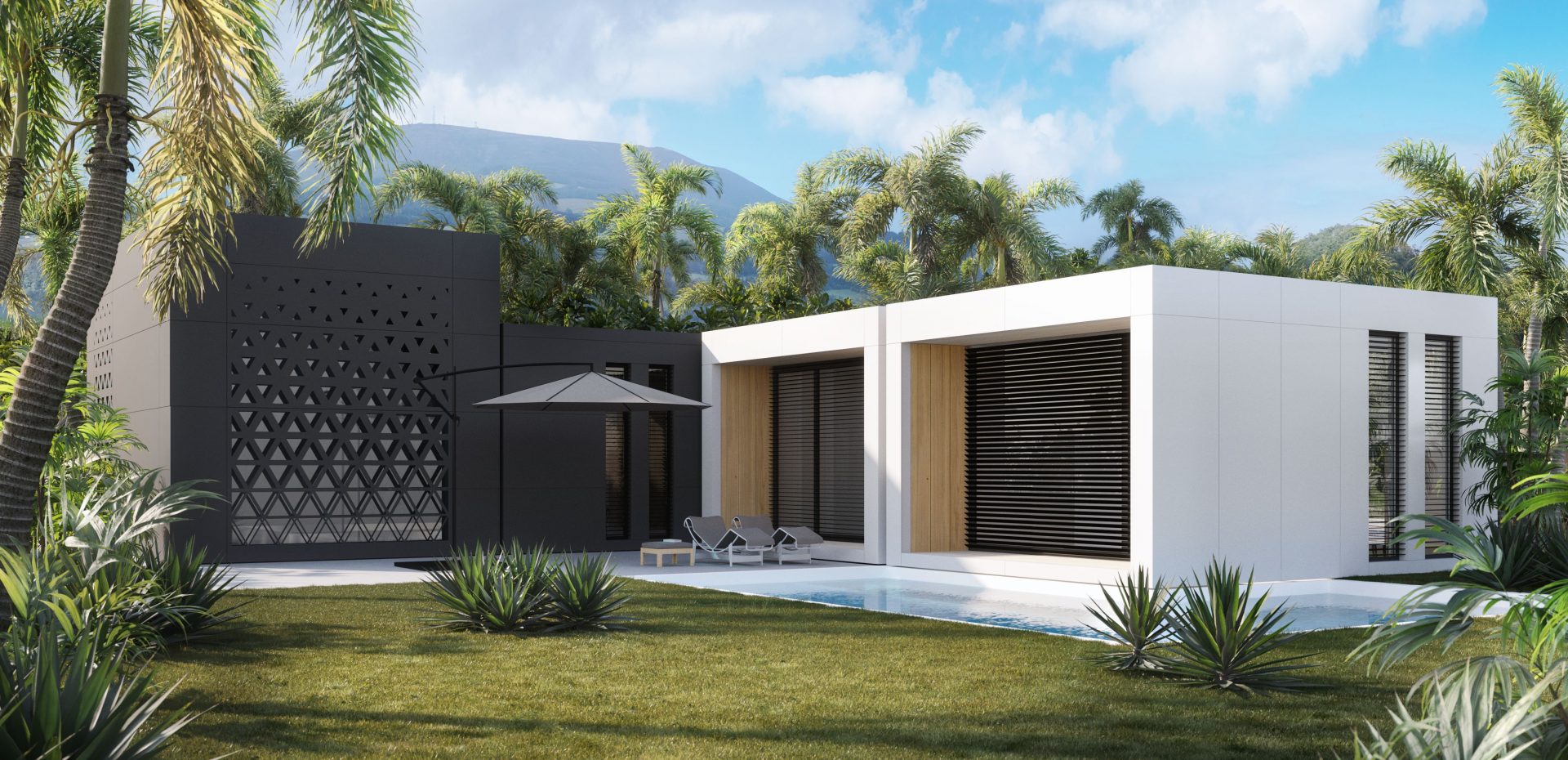
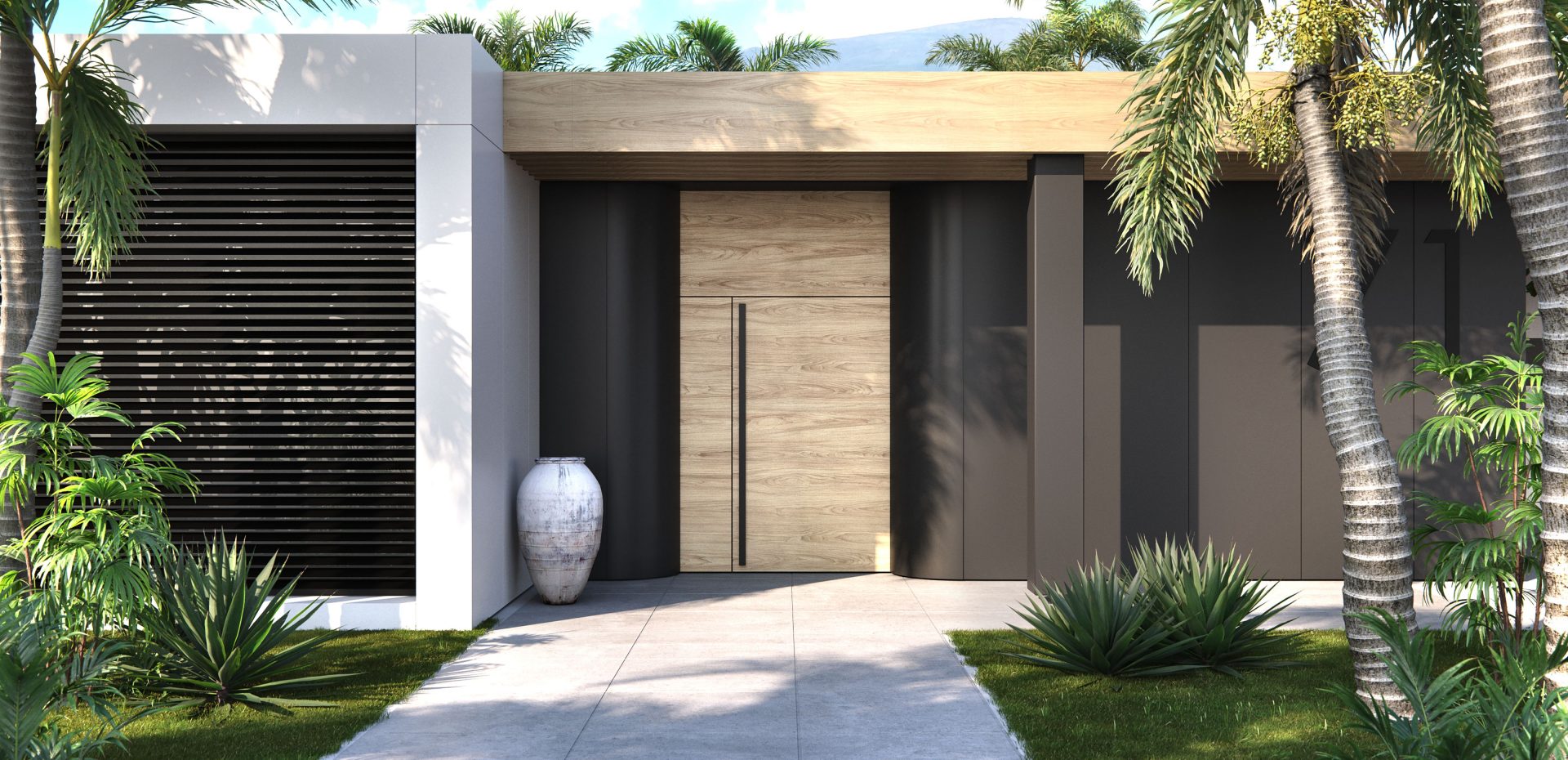